Podcast: How Will USP <800> Impact My Retail and LTC Pharmacy?
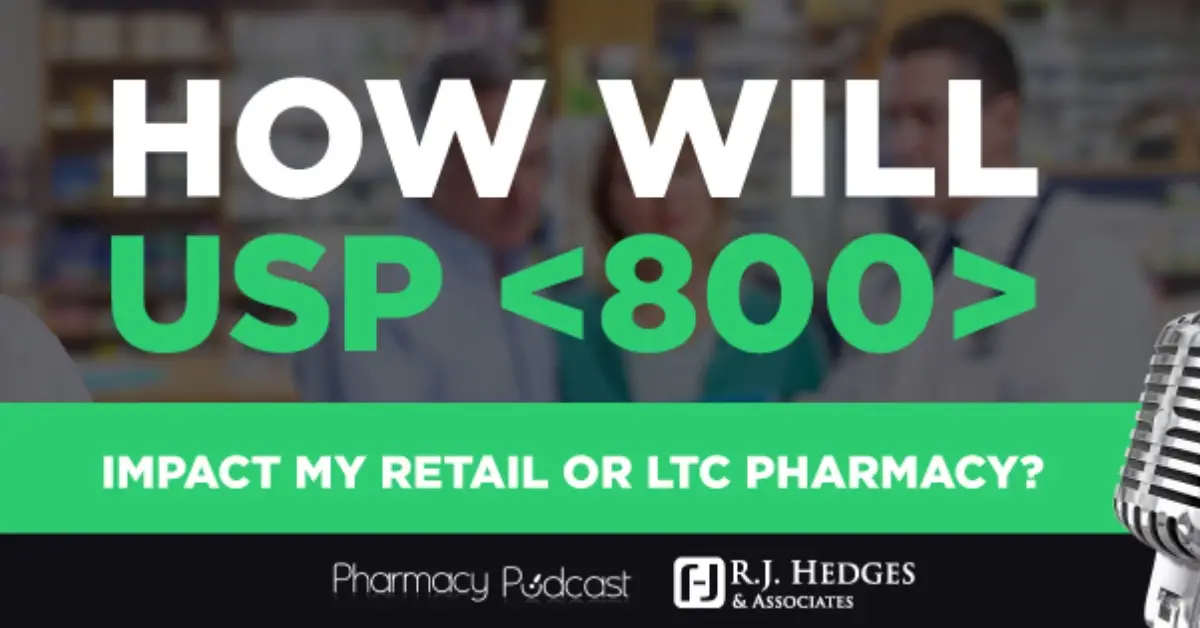
A lot is happening in the pharmacy marketplace, including PBM reform and even massive layoffs. While a lot of this buzz might seem negative, there’s a feeling that positivity is on the way. Still, it’s crunch time for the pharmacy industry with USP <800> on the horizon.
What Are the Basics of USP <800>?
Though USP <800> was delayed once previously, it’s definitely coming into effect in December of this year. USP <800> was designed to address the proper handling of hazardous drugs in the pharmacy setting, and its guidelines are plainly aimed at promoting patient and worker safety in and around sterile and non-sterile compounding.
The first section of USP <800> covers compounding in its purest form. However, this section has also created a lot of confusion because, when looking at section two, you’ll realize that dispensing pills, capsules, liquids, and manufactured packaging items are also covered by USP <800>.
The terms being used to describe hazardous drugs can also be confusing, especially for those that only do compounding on the side, but this is simply the new language and must be learned. These teams include antineoplastic, non-antineoplastic, reproductive risk only, dosage form, risk of exposure, packaging, and manipulation.
What Does a Pharmacy Need to Do First with Their Hazardous Drugs?
First, a pharmacy must identify which hazardous drugs they have in their store. This starts with the NIOSH list of antineoplastics and other hazardous drugs in the healthcare setting. The NIOSH list debuted in 2016, though it’s scheduled for rerelease in December of this year, and it should be your reference guide moving forward.
This list has 42 pages of information and is a truly complete list of hazardous drugs that have been divided into three sets of tables. Table one is all antineoplastic drugs; table two is all non-neoplastic drugs; table three is non-antineoplastic drugs that primarily have adverse reproductive effects.
Pharmacists should use this list to properly identify all hazardous drugs in their pharmacy.
What Should Pharmacists Do Once These Hazardous Drugs Are Identified?
From an operational point of view, the next step should be to use the hazardous drug inventory sheet. It lists the drug name, form of the drug (tablet, capsule, liquid), whether it needs to be reconstituted, whether it’s contained in manufactured packaging, and the NIOSH table number.
After completing inventory of any hazardous drugs, retail pharmacies should then segregate them. Placing these drugs on a shelf or in a section separate from the regular stock is a good idea. As you perform this segregation, you will want to mark the area or shelves with a hazardous drug sign or label.
Changes Under USP <800>
There are several things we do in pharmacies today that we will no longer be able to do thanks to the new standards of USP <800>. For example, if there’s a hazardous drug that is required to be split or crushed, pharmacies won’t be able to do it as of December 1st of this year. The same goes for mixing components together or taking raw components of compounds and mixing the together. All of these actions are required to be prepared inside a negative pressure lab, which will also be known as a containment secondary engineering control (C-SEC).
These negative pressure areas will have to have 12 air changes per minute (ACPM) within the lab. Inside the lab, you will have the new name for a hood, which is containment primary engineering control (C-PEC). These have to be vented to the outside air or have a double HEPA filter system.
Why Must Hazardous Drugs Be Segregated?
In a retail or long-term care pharmacy, it’s not technically mandatory to segregate your hazardous drugs. However, a pharmacy must use separate counting tools for hazardous drugs. If hazardous drugs are segregated, the tools can be stored with them. So, when the technician grabs the drugs off the shelf, they can grab the tools with them and complete the filling process. After, they can properly clean the counting tools and return them to the proper shelf.
If your hazardous drugs are scattered throughout your pharmacy, how will you remember which ones are hazardous and which aren’t? How will you remember to grab the right tools? It can be very confusing if the drugs aren’t segregated.
What If There Are Special Handling Requirements for Hazardous Drugs?
During the initial inventory, one of the items to review is the safety data sheet. These sheets have a personal protective equipment section. No matter what, you’ll have to look at these sheets and identify the type of equipment needed. In most cases, the retail or long-term care pharmacies only need latex gloves for counting pills or pouring a reconstitution as a liquid.
This is drastically different than filling a hazardous drug in a negative pressure room. The personal protective equipment goes all the way up to a personally fitted respirator. That’s whole different standard, but this podcast mostly focuses on retail.
Pill Counters and Robots
For retail, we must consider pill counters and robots. We cannot use hazardous drugs with these mechanisms unless there’s documented proof that they do not stress the medication and create powdered residue when processed.
Right now, when we look at the two big pill counters out there, the Icon Pill Scanner has no mechanical mechanism. It can be used because of the nature of the piece of equipment: scanning. You just take the tray after you use it and you clean it. Kirby Lester are quite close to having a compliant unit; it could potentially be announced in the next month.
On the robot side, there’s only one unit that meets the non-stress requirement: Synergy Medical’s SynMed and SynMed Ultra. Other companies are looking to become compliant, so stay tuned to see what they come up with.
Who is Going to Regulate USP <800>?
With USP <800> hazardous drugs, there are going to be two state and three federal agencies who are going to be enforcing this rule. At the state level, enforcement will come from the state board of pharmacy inspectors and the state department of environmental protection.
Some state board pharmacies are saying that they’re going to delay the implementation or may not adopt the rules at all. However, remember that this is a federal rule that’s going to be enforced and implemented.
Let’s think about the state board. Imagine a pharmacy gets in trouble – like the New England Compounding Center. What is the state going to do? Also, if the pharmacy doesn’t implement USP <800> and there’s an incident, do you think the attorneys are going to look at the pharmacy as negligent for not following a federal guideline?
Now let’s consider the state Environmental Protection Agency. Each state calls it something different, but these inspectors are all trained by the EPA. They will want to know where your Warfarin is, what happens to it when it expires, and whether you quarantine and dispose of it properly.
Many pharmacies have already seen these on-site inspections, especially in Kentucky, Indiana, Ohio, and Pennsylvania. It doesn’t matter whether your state board of pharmacy implements USP <800> or not because the EPA within your state does not follow your state board of pharmacy regulations.
On the federal level, we have the FDA, EPA, and OSHA. Inspections are already happening. An R.J. Hedges client received two write-ups from the FDA, one from USP <800> and one from USP <795>.
What Should You Do Next?
This whole thing is a process. R.J. Hedges started researching and preparing back in January and worked all the way to July to create retail and compounding programs for USP <800>. Though compounding is more complicated, retail is fairly straightforward, and the process takes about a month.
R.J. Hedges walks you through the entire process, but the key part is to start early. If you wait until the end of November, you’ll have some trouble. The program is a customized, step-by-step process that your project manager will walk you through.
This program covers everything. To get started, fill out this questionnaire and our staff will follow up with you quickly.